Dry Ice Production Process & Handling
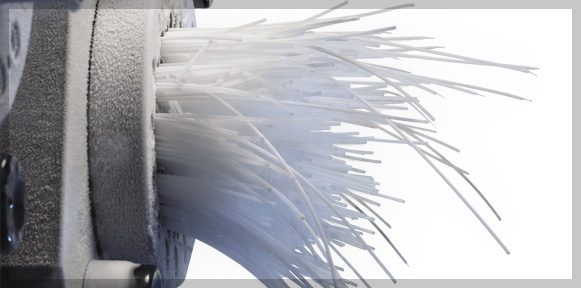
Dry ice is made by taking pressurized Liquid CO2 (LCO2) and allowing it to expand into the natural atmosphere. This causes the LCO2 to expand into both a gas vapor and solid snow. The snow is then either compressed to form blocks or compressed and extruded to form pellets or nuggets. The equipment required to make the dry ice includes a Liquid CO2 tank and a Pelletizer or Block maker.
Production Process Overview
The production process is comprised of the following items:
- LCO2 Vessel:
Horizontal or vertical storage vessel (30 to 60 tons) installed close to the production unit but external to production area - Insulated Lines, LCO2 Filter, & Pressure Regulators:
"K" copper line, rated at 600 psi (40 bar) and wrapped in 2" to 4" of insulation, connect storage vessel to the production unit - Injection:
LCO2 is injected into chambers inside the production machines; creates pressure and LCO2 expands; ~2.3 to 2.5 lbs of liquid CO2 are flashed to make 1 lb of dry ice - Production Unit (Pelletizer, Press, Reformer):
CO2 snow is then compressed, extruded or remolded into a form (pellet, nugget, slab or block) to suit end-user/ industry requirements - Vapor CO2 Exhaust/ Reclaim:
Escaping vapor CO2 can be vented outside of production area or reclaimed, compressed, and liquefied back into LCO2 - Packaging/Storage Tote:
To minimize sublimation loss, dry ice is packed into insulated totes for shipment or immediate use
Shipping & Storage
Due to its low temperature of -78°C (-109°F), dry ice is utilized in all sorts of industries as a cooling medium. It can be used or supplied as snow, pellets, nuggets, slabs, or blocks to suit industry and production needs. Cooling products or parts during the shipping process is a common application for dry ice.
There are several key considerations to keep in mind when shipping dry ice:
- Different needs and applications call for different types of dry ice
- Dry ice pellets and nuggets are typically used for smaller packages and shorter distances
- Dry ice slabs work great for airline catering – fit cart and have slow sublimation rate
- High quality insulated containers are needed to reduce sublimation and keep products safe
- Durable polystyrene containers work the best
- Styrofoam coolers break easily and are therefore not good insulators
- Plan on losing 3% - 8% of dry ice due to sublimation every 24-hour period due to sublimation
- The rate of sublimation depends on type of dry ice, outside temperature, air pressure, and quality of packaging
- When packing dry ice with products in a container, place the two items as close together as possible, filling empty space with wadded newspaper or other packing materials
- Dead-air-space will cause the dry ice to sublimate faster

Dry Ice Safety Tips
Handling
- Dry ice is extremely cold and should never be touched by bare skin (may cause frostbite)
- Use gloves or a towel when handling dry ice to minimize skin exposure
Storage
- Store dry ice in an insulated container to minimize sublimation (thicker, better insulation = less sublimation)
- Do not store in unventilated areas; the dry ice sublimates into large quantities of CO2 gas, which displaces oxygen and increases the danger of asphyxiation
- Do not store dry ice in a completely airtight container; the container may explode due to sublimation and CO2 expansion
- Do not store in a freezer - the coldness of the dry ice will shut off the thermostat and freezer
Ventilation
- Use dry ice in a well-ventilated area to prevent the build-up of toxic CO2 levels
DRY ICE PRODUCTION
- All About Dry Ice
Learn about dry ice. - Making & Handling
See how dry ice is made. - Making vs Buying
Should you make or buy the dry ice you use? Find out here. - Dry Ice for Cleaning
See how dry ice is used for industrial cleaning. - Dry Ice for Packaging
Using dry ice for packaging and shipping. - Dry Ice for Processing
See how dry ice is being used in the processing and manufacturing industries. - Buy Dry Ice
Contact Cold Jet to find a dry ice supplier near you.